SLIDING BEARING
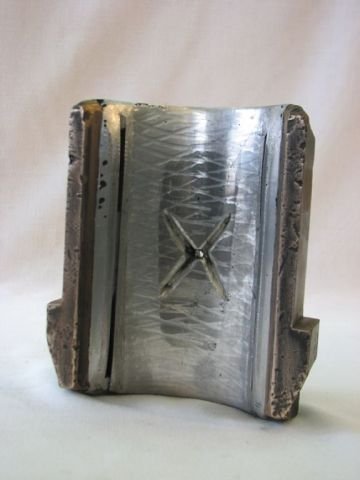
-
Item owner - FNM
-
Category - FNM Collection
-
Inventory - 0135
-
Author - Ferrovie Nord Milano
-
Dimensions - 15x20x4 cm
-
Dating - 1879-1958
A semi-cylindrical shell covered on the inside with a special anti-friction alloy of tin, lead and zinc (referred to as S alloy or white metal: a special anti-friction alloy of copper and tin, covered with white metal with a low melting point). A series of grooves in it communicate with a lubrication pipe through a central opening. The grooves are referred to as “spider legs”.
It acted as a sliding roller bearing.
It rested on the stub axle of a railway axle inside the bushing, adjusted in height by brass plates placed between the bearing and the upper inner wall of the body of the bushing. The raised supporting surface and the considerable weight supported required a considerable amount of lubrication, which was guaranteed by the grooves. The anti-friction material, which has a much lower melting point than the shell to which it is applied, was obviously consumed over time.
Skilled workers worked the anti-friction material poured over the inner surface of the half-shell. This skill could only be developed with considerable experience. The thickness of the layer depended on the type of stub axle with which
it was to be paired. All the operations involved in working the surface were manual, as was groove formation. Abrasion and filing altered the thickness at certain points, requiring familiarity with the specific way the case moved on the bogie.